Did you know that you can optimize your MIG welder’s performance through proper and timely maintenance of the liner?
The liner is responsible for guiding the welding wire from the feeder through the gun and the machine’s contact tip.
Without it, your welding wire will not be able to reach its destination, hindering performance and, in some cases, may cause the machine to stop working entirely.
For the smooth delivery of your welding wire and the machine’s overall health, it is important to learn how to clean a MIG welder liner properly.
Why Is Your MIG Welder Not Working?
Before we talk about cleaning a MIG welder liner, you must know why it is having issues in the first place.
Knowing the possible reasons why it requires regular maintenance will give you a better grasp of how your machine works.
Here are some of the reasons your MIG welder is malfunctioning:
1. Neglecting Maintenance Protocols
Like any machine, if you want your MIG welder to perform at optimal levels, you must maintain a strict maintenance regimen.
Often, this includes the use of a MIG welder wire cleaner.
Regularly cleaning the liner means it will not get dirty and, ultimately, malfunction, which can be costly to address in most cases.
2. Reshaped Wire
Liners are an integral part of your welder.
As mentioned, they are responsible for guiding the welding wire through the gun nozzle and into the tip.
If the liner is tampered with, such as bent unnecessarily or in an unfavorable direction, it can lead to problems with the welding spool.
These problems include delays in wire feeds and commonly occurring bird’s nests.
Additionally, the liner may bend into the wire, causing friction and reducing the amount of welding pool produced.
3. Liner Type, Size, and Length
The type, size, and length of the liner affect its overall functionality and lifespan.
You must choose the correct liner to match the metal you are planning to weld with.
Remember, Teflon liners are used for aluminum and Teflon steel-coated ones for steel welding requirements.
The application of these different types of liners also varies.
For instance, aluminum is a lightweight metal and moves much quicker than steel.
Therefore, the Teflon liner must be attached closer to the drive rolls, with some provision kept for the liner to extend outwards a little.
On the other hand, steel is much firmer.
As such, liners for steel will have a ferrule at the end, which will get locked down when screwed back up.
Additionally, the size of the liner matters and should match the diameter of the wire; otherwise, it will result in tangled wires.
How To Clean a MIG Welder Liner
If you use your welding machine often, it is better to clean it every week to make sure its performance is not compromised at any point.
With the factors that cause the welder liner to get dirty identified, here is an easy-to-follow guide to cleaning a MIG welder liner:
Step 1: Unscrew the welder liner’s nut.
To reach the liner, you first need to unscrew the nut holding it within the welder.
Still, the liner is securely held behind the welding wire and the welding tip.
This means you will also need to remove both of these pieces from the machine.
As a novice welder, it is recommended that you align the pieces you remove on your workbench.
In this way, you can easily remember the proper order when putting it back.
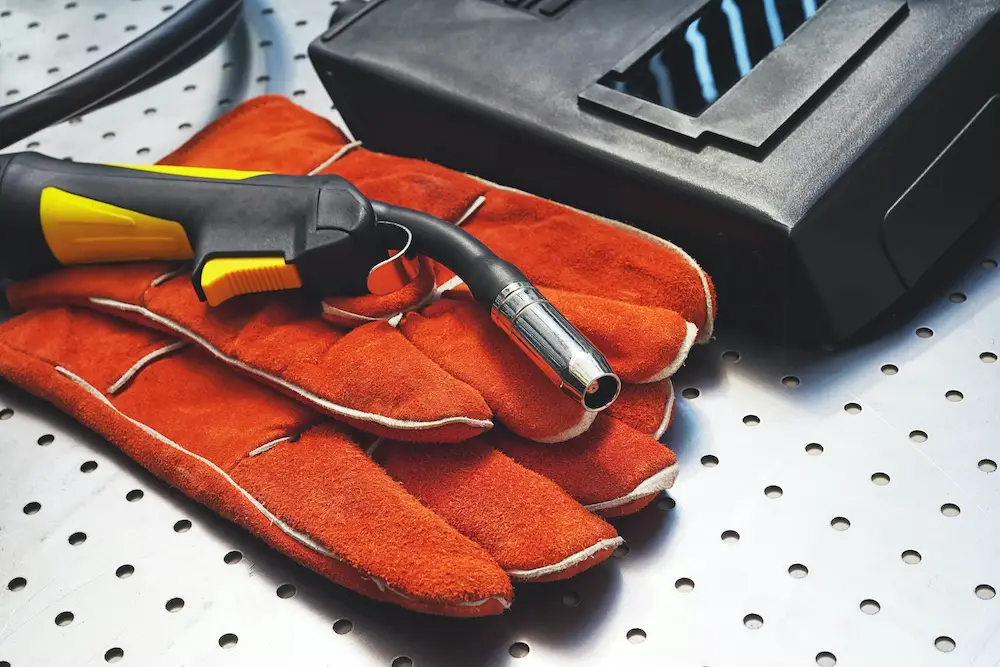
Step 2: Use compressed air.
The most common kind of MIG wire cleaner is compressed air blown through in short bursts.
This process forces dust and metal particles to leave from either end without causing buildup.
Such buildup typically occurs when using a lubricant-based MIG wire cleaner.
As a general rule of thumb, it is advised you do not use lubricant-based cleaners, as these tend to attract dirt rather than clean the machine.
More than that, they can cause rusting or fast wear and tear of the system.
Step 3: Inspect the liner for damages.
Since you already have the liner in your hand, it is a good idea to check it for potential kinks and nicks that may reduce optimal performance.
If the liner is too damaged, it will create a drag in the welding wire and cause delays in the wire feed.
Eventually, it will clog the tip cover and cause a buildup within the welder.
Step 4: Replace the liner or put it back.
Rather than using the damaged liner, it is a good idea to replace it entirely.
Thankfully, welding liners do not cost much.
Replacing them at the right time will protect you against other overhead costs in the future that may occur because of some underperforming damaged liner.
Upon inspection, and if you think the liner is now cleaned thoroughly and good to go, it is time to put it back into the welder.
As you may already know, this is a delicate process.
Again, it is a good idea to either document the removal process or align the parts so that you can remember the order accurately when putting them back.
Make sure the gun is aligned correctly against the liner to protect it against any potential hits and kinks.
Then, use slow and carefully judged movements so that you can gently place the liner back in its place.
Finally, use a spanner to screw the necessary nuts back into place.
Conclusion
MIG welders are one of the more expensive tools you will own as a professional or amateur welder.
You can use it for a variety of projects, from home repairs to renovations.
Therefore, maintaining it regularly using a MIG welder wire cleaner will ensure not only a long life but also optimal performance.
On the other hand, an ill-kept welder with a dirty liner will damage the system and create untidy welds, which you may need to correct over time.
Hence, if you want to save yourself the extra hassle and trouble, learning how to clean a MIG welder liner will prove beneficial in the long run.