Like any piece of machinery, MIG welders also come with their fair share of troubles that need to be addressed in a timely fashion.
One of the most commonly occurring issues involves MIG welder wire feed problems.
If the wire in your MIG welder is not feeding properly, you may experience frustration and burnout, which can negatively affect the progress of your work.
MIG Welder Wire Feed Problems
Think of the wire feed system like the nervous system in your body.
Any issues with its functioning will lead to a domino effect, where the whole system will come down crashing.
If you find your MIG welder not feeding wire, here are some of the places to look for commonly occurring issues:
1. The Spool Hub
The spool hub is the source of your wire feed.
The spring system incorporated into the hub ensures a braking mechanism to prevent over spooling.
Similarly, you do not want your wire feed over-tensed either.
The best way to check the level of tension on your spool is to pinch it forward so that it reverts back into the feed with a snap.
This pressure that the feed experiences will help you determine whether the spool requires any additional tension or not.
2. Drive Rolls Should Match the Wire
It is important to understand that you are using the correct drive rolls according to the diameter of the welding wire.
Most of the models tend to have provisions for running two different kinds of wire sizes.
Make sure each of these is adequately aligned with the wire you are using.
In this way, there isn’t a lot of tension that deforms the wire’s properties and causing feeding problems.
Additionally, using the correct type of drive roll to match the wire you are using is also important.
For instance, U-grooved drive rolls are preferable for use with aluminum or other softer metal wires.
3. The Wire Feed Liner
The proper maintenance of your wire feed liner goes a long way in determining the lifespan of your MIG welder.
In addition, it also helps avoid wire feed problems.
Over time, the liner will accumulate dust and grime, which can create wire feed problems.
With the MIG welder not feeding wire, you should consider cleaning your feed liner.
This can be done via pumping compressed air in short bursts to get rid of any clogged regions within the liner.
Another commonly occurring issue with the liner involves the liner separating from the welder’s body.
This is primarily due to the welder being used in different positions that may put unnecessary strain on the liner.
Users have the option of replacing the liner entirely or investing in maintenance regimens, including compressed air and cleaning pads.
Most professionals discourage the use of cleaning pads due to the exposure of the liner to excessive moisture, which can attract dust.
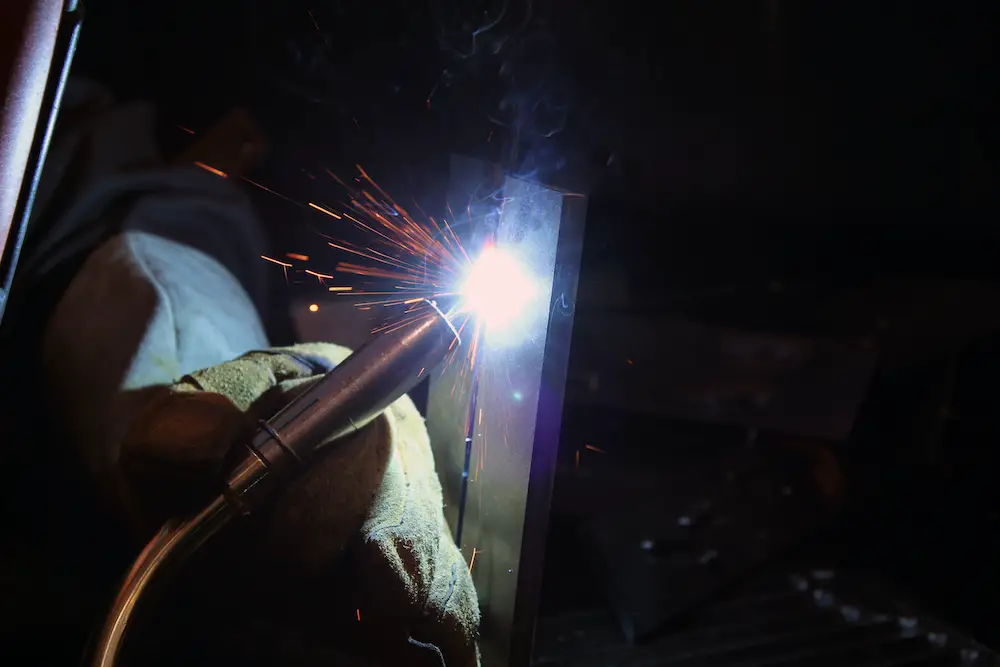
4. Correct Contact Tip
The size of your contact tip should adequately match the diameter of the wire you are using for your welding needs.
If you are trying to use variable sizes, the welding arc will not turn out the way you are expecting it to.
The wire feed exits through the contact tip and into the welding pool.
Therefore, if the contact tip gets clogged or distorted, the welding pool and the formed bead will be affected.
Other than that, if your contact tip is beyond repair, we suggest changing or replacing it.
5. Quality of the Welding Wire
If you have not been using your welder for a while now, chances are, the wire feed has experienced weathering and may be rusty.
This can cause the liner to clog up, creating wire feed problems.
If you are sure there is rust on your spool, try unspooling the wire until you get to the point where there is no more rust.
You can also try to reduce the level of moisture that the wire may experience over time by unspooling it and patting it dry with paper or cotton material.
If the wire is beyond repair, unfortunately, you will need to replace the entire spool, which can be costly.
As a good rule of thumb, try to adhere to a basic maintenance regimen that will help you save a lot of money.
First Aid for Wire Feed Troubles
We strongly believe in both top-to-bottom and bottom-to-top problem-solving approaches.
Hence, we have also put together a list of potentially occurring problems during your use of the MIG welder.
These are followed by solutions that involve either replacing, adjusting, or cleaning certain regions to resume working flawlessly with the MIG welder.
If you see any of these issues with your MIG wire feed welding machine, follow the first aid guidelines given below for a speedy recovery:
1. Birds’ Nests
- Clean the wire feed liner with bursts of compressed air.
- Remove obstruction from contact tip.
- Adjust the tension on the drive roll.
2. Drive Roll Slipping
- Adjust the spool hub tension.
- Change and match the contact tip to the wire feed.
- Adjust the tension in the drive roll.
3. Inconsistent Arc
- Release tension from the spool hub.
- Change the contact tip and replace it with one matching the diameter of the wire being used.
- Adjust the drive roll tension.
4. Burn Back Effect
- Check if the spool wire is binding.
- Adjust the tension in the drive rolls.
- Release tension from the spool hub.
- Replace the contact tip to match the diameter of the wire being used.
5. Wire Feed Not Passing Through
- Replace the contact tip.
- Replace the gun liner.
Conclusion
MIG welder wire feed problems are a direct reflection of how well you maintain and look after your MIG wire feed welding machine.
The proper and timely maintenance of the machine, as well as choosing the best consumables, can go a long way in determining the quality of weld it is capable of undertaking.
In the end, wire feed problems are manageable.
If not contained, though, they may lead to costly repercussions, including replacing expensive parts, such as the welding wire, the contact tips, and the gun liner.