Contrary to popular belief, a MIG welder wire feed motor not working is actually a commonly occurring issue with many models.
In fact, Miller MIG welder wire feed problems often have a domino effect.
This means that a simple issue may cause additional problems, such as overhead costs due to late delivery and unnecessary downtime.
Most importantly, you also need time to figure out where and why the welder is experiencing wire feed problems.
MIG Welder Wire Feed Motor Not Working
Below, we have put together a guide to help you figure out the possible reasons why the wire feed motor in your MIG welder is not working.
For starters, there are a few places you can check for obstructions, wear and tear, and maintenance.
1. Wire Quality
Does wire quality even matter when it comes to MIG welders?
Many people tend to negate the fact that wire quality affects the wire feed motor and keep it from working.
In truth, most MIG welder wire feed problems often originate at this point.
Factors such as moisture accumulation due to low maintenance or long periods of inactivity can lead to weathering and cause rust, which ultimately will clog your system.
If you can identify rusting as the leading cause, try to unspool the wire feed until you reach a clean segment of wire to use.
Maintaining the wire feed motor goes a long way in determining the worth of your machine.
Basic maintenance tips include dabbing your wire with a garbage bag or a blanket after taking it out of the motor.
2. Tension in the Spool and Drive Roller
Most Miller MIG welder wire feed problems arise at the point of your spool brake and drive rolls.
If there is too much tension in your wire spool, it will lead to fast wear and tear.
On the other hand, if there is very little tension in the spool, you will have a bird’s nest mess at your hands to deal with.
With this in mind, it is crucial to maintain a certain level of hub tension to allow the wire spool to turn comfortably.
Similarly, if your drive rolls are under a lot of pressure, your wire can permanently deform by flaking out and damage your wire feed motor.
A deformed wire will also be counterproductive to the contact tip and may reduce overall feed capacity.
While there is no exact unit of measurement defining the level of tension adequate for your wire spool, there are few tips you can use to reach an optimal level.
- Try loosening the drive rolls and adjusting their alignment to align against the gun’s inlet properly.
Then, increase the tension while also feeding the wire over another holder, such as a wooden block.
Keep increasing the tension until you are a half turn away from the wire slipping off the holder.
- Keep an eye out for any potential signs of wear and tear your wire may have experienced over time.
For instance, if you need to tighten the wire more than usual, check if your feed meets all the necessary parameters and settings.
If everything checks out, and you still find the MIG welder wire feed motor not working, perhaps your drive rolls need to be changed out.
- Make sure the inlet guides leading to the gun match the size of the wire being used.
These should be aligned, without any grooves, and of the correct size to reduce problems in the wire feed motor.
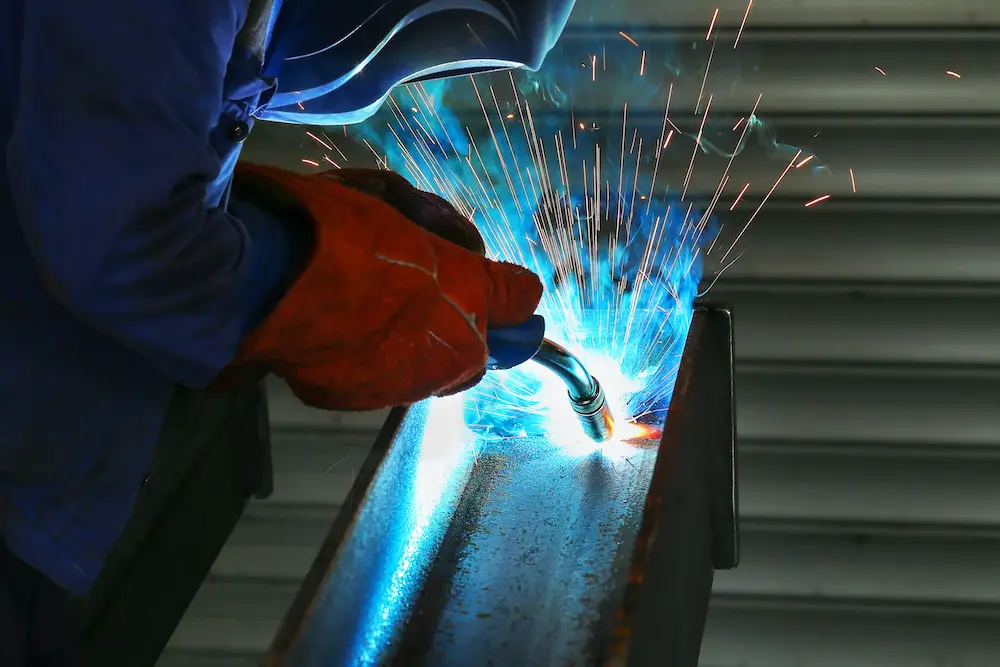
3. Gun Liner Maintenance
The gun liner needs to be squeaky clean if you want to avoid MIG welder wire feed problems.
Again, it also has to be an adequate matching size for the wire being used.
If your wire spool is over-tensioned, it will wear and tear by losing flakes that will accumulate over time within the gun liner.
Often, users tend to lubricate the wire being fed into the gun under false pretense.
The problem is that this can cause the wire to be damp for longer periods, leading to rust accumulation and causing faster wear and tear.
Here are a few things you can do:
- Use low-pressure compressed air to blow into the liner so that unnecessary particle accumulated clogs can easily open up.
- Gun liners are inexpensive and should be regularly replaced to avoid unnecessary MIG welder wire feed problems.
4. Contact Tip Maintenance
Contact tips are one of the essential features of MIG welders.
These are in direct contact with the welding puddle and can become distorted over time.
Additionally, the welding spatter can also lead to wear and tear and clogging.
Here are a few things you can do to address this issue:
- Make sure the wire size aligns with the contact tip ID.
Over time, because of the tip’s direct contact with the welding puddle, the size can become distorted.
- Check if there are any grooves in the tip. This is usually due to excessive drive roll tension.
- Replace the contact tip regularly to increase the overall quality of the welds and add to the machine’s longevity.
If you find that, even after going through the list of possible causes, the wire feed is still giving you problems, get in touch with the manufacturer.
More than anyone, they can give the professional help that your MIG welder requires.
Most of the time, the dealer you have bought your welder from will provide you with a maintenance service.
However, those that don’t will direct you to the manufacturer’s servicing unit.
Conclusion
There can be many reasons behind a MIG welder’s wire feed motor having problems.
Often, learning how to avoid these issues will occur while on the job.
The regions of inspection and maintenance will provide you with a starting point.
However, there may be many other issues that can arise as you go about applying them.
Like any machine, the key is to keep it in working condition through proper maintenance.
Also, it is important that you keep it in the right environment and use reinforcers before putting it in storage.